
Especially for dry bead mills, it is hard to say that they are well known. However, bead mills have a short history compared to other types of grinders. Therefore, their future application is highly expected to respond to the requirements of various grinding operations by the current industry. In principle, bead mills can provide grinding conditions under a high packing density and high energy density of the media as well as cover a broad range of output. Thus, various grinders have been evolved and produced in a variety of shapes to meet changing needs. Though the grinding operation is a unit operation that has been known for a long time, it still often occupies an important position in industry. PB303 Study on the Effects of Grinding Factor and Scaling up in Grinding Using Horizontal Dry Bead Millġ Institute of Fine Particle Technology, Ashizawa Finetech Ltd, Oyama, Japan It can be found that the distribution of temperature inside the reactor was very uniform, the difference in axial temperature is less than 3K, the difference in radial temperature is less than 1K. Furthermore, the distribution of temperature inside the reactor was predicted by CFD. To reduce the deposition of catalysts inside the large slurry bed reactor, the position of inlet of residue oil was optimized. Then, the flowing and distribution of fluid and deposition of catalysts were simulated by CFD. Based on the results of a pilot plant, an industrial hydro thermal cracking reactor of residue oil was developed.
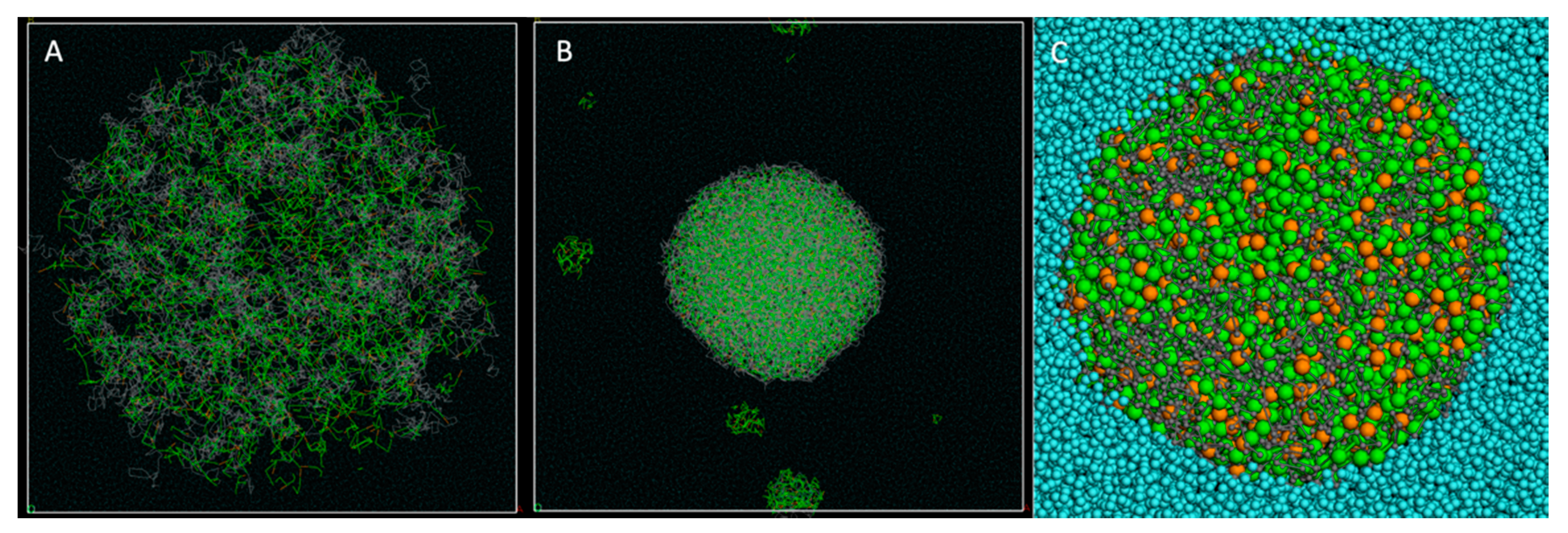
The distribution of velocity and temperature inside the reactor is essential for reducing precipitation of unstable compounds, and preventing reactor from blocking. The precipitates will be attached at the surface of catalysts and reactor, which will lead to the deposition of catalyst and blocking. With the increase of conversion, the stability of residue oil becomes weaker, and some unstable compounds may be crystallized easier. Because of a few catalyst loading, low cost, and low blocking probability, the slurry bed is better to be applied in processing residue oil, especially for heavy residue. Hydro thermal cracking process of residue oil is an important technical route in the area of heavy oil processing. SINOPEC Research Institute of Petroleum Processing, Beijing, China

PB302 Numerical simulations of flow and heat transfer in a industrial hydro thermal cracking reactor of residue oil On the whole, the rigid-flexible impeller could enhance the suspension of solid particles effectively. It was also suggested that longer flexible material and longer mixing time results in well homogenous distribution of solid particles in the tank equipped with rigid-flexible impeller. The suspension of solid particles in the rigid-flexible impeller system was more homogeneous.

It turned out that the structure of impeller has an obvious effect on solid particle distribution. The effects of impeller type, length of flexible material, connect way of flexible material, mixing time were investigated by using the Eulerian–Eulerian two-fluid model and the standard k–ε turbulence model.
#MODELING NANOPARTICLE DROPLET MATERIALS STUDIO SOFTWARE#
The software of Fluent was utilized to investigate flow field structures in stirred tank. Particle suspension characteristics are predicted computationally in a stirred tank with solid concentration of 25% and driven by rigid-flexible impeller. School of Chemistry and Chemical Engineering, Chongqing University, Chongqing

Xia XIONG, Zuohua LIU, Liang WANG, Changyun TAO PB301 Numerical simulation of particle suspension in a stirred tank equipped rigid-flexible impeller
